The Rise of ES Fiber
In recent years, ES (ethylene–propylene side-by-side) fiber has gained significant traction in the nonwoven industry. Characterized by its core-sheath structure—where the sheath has a low melting point and the core offers mechanical strength—ES fiber performs exceptionally well in thermal bonding processes like hot air-through. This makes it ideal for hygiene products, insulation materials, and filtration applications.
Traditionally, ES fibers are categorized by material combinations such as PE/PP or PE/PET. However, as sustainability becomes a top priority in the textile and materials industry, the environmental footprint of synthetic polymers is increasingly under scrutiny. This is where PLA (polylactic acid) bi-component staple fibers enter the conversation.
Why Consider PLA Bi-component Staple?
eSUN’s PLA bi-component staple fiber is crafted entirely from bio-based PLA and designed with a core-sheath structure. The sheath consists of low-melting PLA offering softness and thermal bondability, while the core provides durability and strength through high-melting PLA.
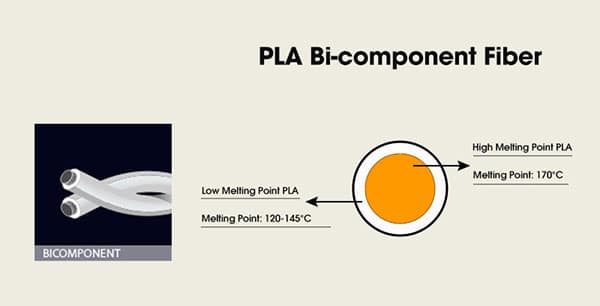
When heat is applied, only the outer layer melts, bonding the fibers together without the need for chemical adhesives. This natural fusion process results in a strong, form-stable nonwoven material with no added toxins—an eco-conscious solution that is hypoallergenic and safe for skin contact.
Key Benefits of PLA Bi-component Staple
- Fully Biodegradable: Made from renewable plant resources, PLA Bi-component Staples decompose under industrial composting conditions.
- Adhesive-Free Bonding: No chemical binders are required, eliminating potential allergens and irritants.
- Multi-process Compatibility: Compatible with various nonwoven techniques such as spunlace, air-through bonding, needlepunch, wet-laid, and more.
- Thermal Stability: Maintains fiber structure and product integrity after bonding.
- Natural Skin-Friendly Properties: Excellent breathability, antibacterial behavior, and moisture regulation.
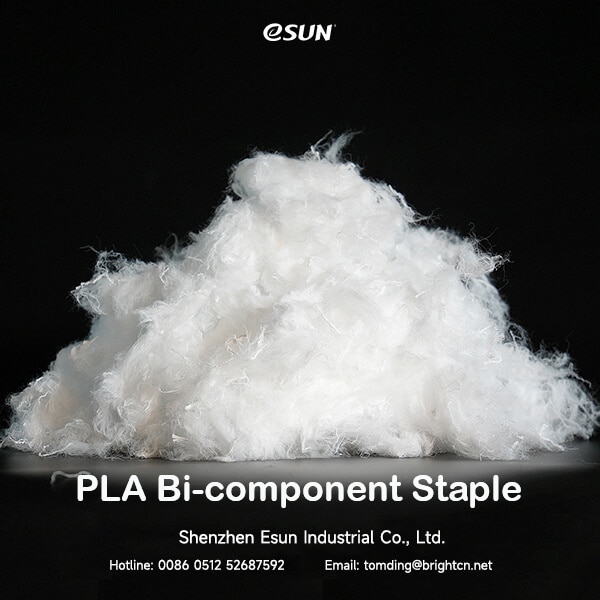
Versatile Applications Across Industries
1. Nonwoven and Hygiene Products
Thanks to its softness, lightweight nature, and thermal bonding capabilities, PLA bi-component staple is a perfect fit for sanitary items like diapers, sanitary pads, underpads, and more. It’s also ideal for the top and bottom layers of these products when combined with natural fibers, adding strength and comfort.
Processed through air-through, calendered, or needlepunch methods, these fibers can be used in fast-moving consumer goods, medical packaging, and even protective apparel.
2. Thermal Bonding without Chemicals
In applications where strength and softness must coexist—like absorbent layers in sanitary products—PLA bi-component fibers outperform traditional bonding agents. They support point-bonded nonwoven structures, delivering better bulk, resilience, and fluid absorption.
Furthermore, when mixed with natural fibers like cotton or hemp, PLA fibers enhance breathability and antibacterial performance while improving structural integrity.
3. Filling and Cushioning Materials
The differential shrinkage of the core and sheath after heat processing creates natural 3D crimping in the fibers. This makes them ideal for filling pillows, stuffed toys, mattresses, and insulation. Their hypoallergenic and antibacterial properties make them suitable for baby care, eldercare, and pet products.
4. Beyond Hygiene: Broader Use Cases
PLA bi-component staples are also applied in:
- Eco-friendly filter media
- Sustainable packaging
- Agricultural textiles
- Rigid boards and panels
- Automotive interior padding
A Path Toward Sustainable Innovation
As industries look to reduce plastic dependency and embrace bio-based alternatives, PLA bi-component staple fibers are emerging as a compelling replacement for traditional ES fibers. They meet growing environmental demands while delivering comparable—if not superior—performance across various applications.
With eSUN’s proven manufacturing capacity and commitment to innovation, PLA bi-component staples are ready to support the textile and nonwoven sectors’ green transformation.